What is Root Cause Analysis?
A root cause is an element that contributes to nonconformance and ought to be permanently removed via process improvement. The root cause of the problem is the underlying issue that started the chain of events.
The concept of root cause analysis (RCA) refers to various methods, instruments, and procedures used to identify the root causes of issues. Some root cause analysis (RCA) methodologies are more focused on determining the actual reasons for an issue. Other RCA methodologies are more generic problem-solving approaches.
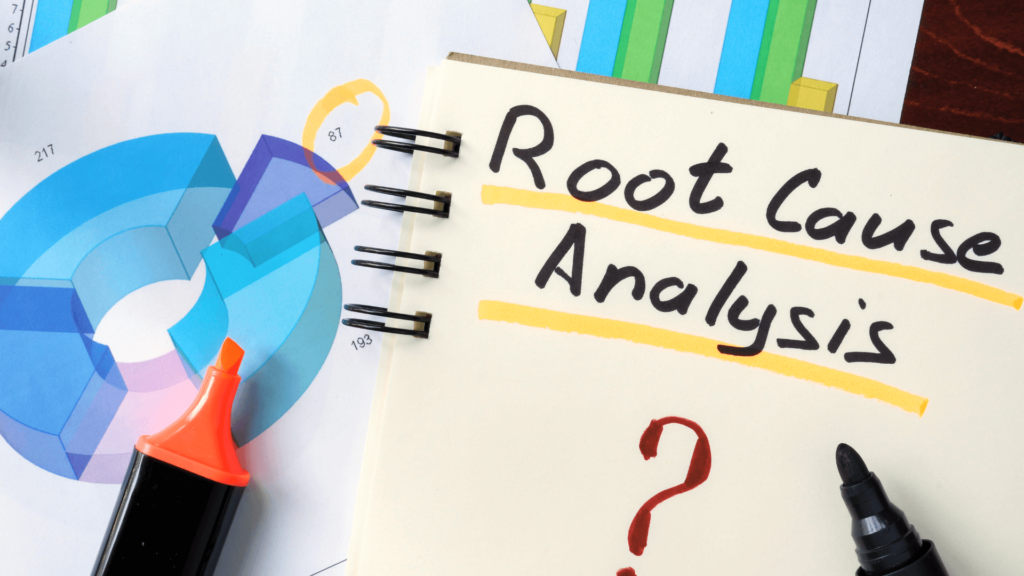
What Does a Root Cause Analysis Do?
Root cause and impact analysis is the process of searching for the underlying causes of issues, identifying the best strategy to fix flaws and finding a solution that can be used to stop the recurrence of the problematic event.
The strategy encourages all efforts to identify the actual reasons behind process flaws or obstructions and address them to make improvements over time.
A prevention strategy can be successfully developed using the RCA approach to determine a problem’s underlying causes and contributing variables. Root cause and impact analysis is useful for incident management, maintenance problems, productivity problems, risk analysis, barrier analysis, etc.
What Advantages Does Root Cause Analysis Offer?
The root cause analysis method aids in identifying and describing a problem’s root cause(s). RCA may provide a productive, organized approach to problem-solving by getting to the root of a problem and looking at all of its components.
The problem-solving technique helps companies and processes by forcing them to dig deep into a problem and develop long-term solutions because of this preventive feature.
Additionally, it develops a prevention strategy and pinpoints areas for organizational development. Of course, RCA has benefits and drawbacks. So let’s take a look at them.
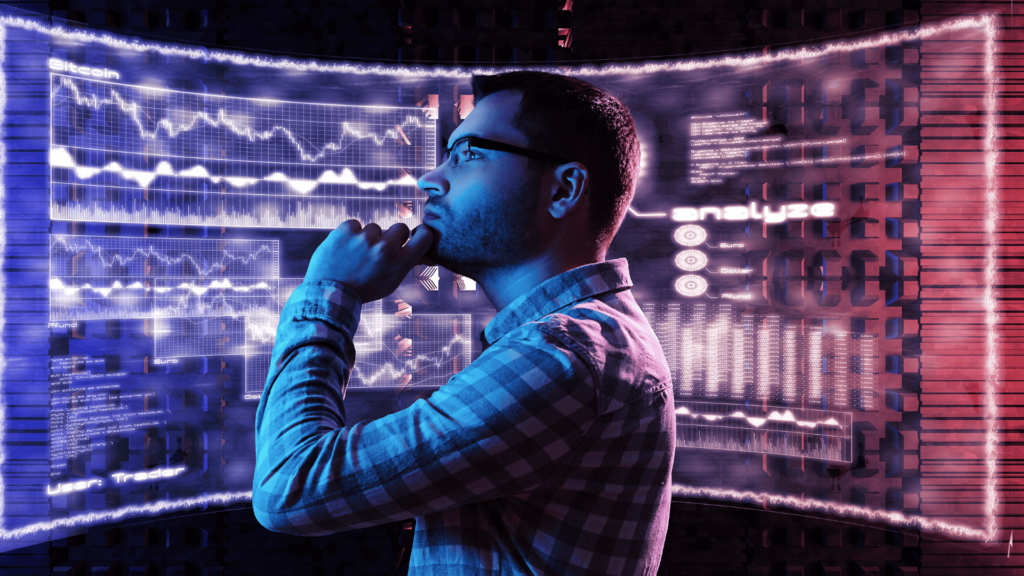
Fundamental Ideas of Root Cause Analysis 💡
Effective root cause analysis is guided by a few fundamental ideas, some of which should be obvious. These will improve the analysis’s quality and assist the analyst in gaining the confidence and support of patients, clients, and stakeholders.
- Instead of just treating the symptoms, concentrate on addressing the underlying causes.
- Don’t discount the significance of addressing symptoms if you only need temporary relief.
- Recognize that there may be – and frequently are – many basic causes.
- Instead of focusing on WHO was at fault, consider HOW and WHY something occurred.
- Be meticulous when locating specific cause-and-effect data to support your claims about the core cause.
- Give enough details to determine a course of action for correction.
- Consider how a root cause might be avoided (or repeated) in the future.
As the aforementioned guidelines demonstrate, it’s critical to adopt a thorough and holistic approach when analyzing complex problems and their root causes. It should work to provide context and facts that will lead to an action or a choice in addition to identifying the core cause. Always keep in mind that sound analysis is actionable.
Guidelines for Conducting a Successful Root Cause Analysis
Root cause analysis is crucial in continuous improvement and a more general problem-solving procedure. Root cause analysis is, therefore, one of the fundamental pillars of an organization’s continuous improvement efforts.
It’s crucial to remember that root cause analysis alone will not result in quality improvement; it must be integrated into a bigger effort to solve problems. The following three guidelines will help you conduct a root cause analysis effectively.
1. Get a Team Together and Some Fresh Eyes 👀
Any additional eyes, whether it be a single partner or an entire team of coworkers, will speed up the process of finding solutions and prevent bias.
2. Make Plans for Upcoming Root Cause Analysis 📝
Understanding the method is crucial as you conduct a root cause analysis. Make a note. Inquire about the analytical procedure in general. Find out if a particular strategy or method suits the demands and conditions of your particular organization.
3. Keep in Mind to Do Success-related Root Cause Analysis as Well ⭐
Root cause analysis is a fantastic method for identifying the source of a problem. The root cause of success can also be determined via RCA, which is normally used to diagnose issues.
Finding the reason why something is working out well is rarely a terrible idea if we can identify the cause of success, overachievement or an early deadline.
This kind of study can aid in prioritizing and proactively protecting important aspects, and we might be able to apply the lessons learned from one sector of the company to another.
4. Procedures of a Root Cause Analysis 🔍
It’s crucial to keep the following in mind while using root cause analysis methods and procedures:
- While a single person can utilize various root cause analysis methods, the results are typically better when several individuals collaborate to identify the reasons for the issue.
- The analysis team that sets out to find the root cause(s) should have significant members who will eventually be responsible for eliminating them.

The following are some steps that a typical root cause analysis in an organization might take:
- It is decided to put together a small team to investigate the root cause.
- Team members are chosen from the organizational department or business process that is having problems. The following could be added to the group:
- A line manager has the power to make decisions and implement solutions
- A problematic internal consumer from the process
- If the other team members have limited expertise with this type of job, a quality improvement expert should be brought in.
- About two months pass throughout the analysis process. Equal weight is given during the analysis to identifying and comprehending the issue, coming up with potential reasons, dissecting causes and effects, and coming up with a solution.
- The team meets at least once weekly, perhaps twice or three times during the analysis period. Since the sessions are intended to be creative in nature, they are always kept brief, lasting no more than two hours.
- A team member is responsible for ensuring that the analysis moves forward or that assignments are distributed among the team members.
- Depending on what is involved in the implementation process, it may take anything from a day to several months until the change is complete once the solution has been established and the choice to adopt has been made.
Root Cause Analysis: How to Perform It
For conducting root cause analysis, there are numerous methodologies, approaches, and techniques available, such as:
- Events and causative factor analysis: This methodology, which is frequently used for significant, single-event issues like a refinery explosion, employs evidence collected swiftly and meticulously to create a timeline for the events leading up to the catastrophe. The causative and contributory elements can be found once the timeframe has been defined.
- Change analysis: This method might be used when a system’s performance dramatically changes. It looks into adjustments made to people, tools, information, and other things that may have caused a change in performance.
- Barrier analysis: This method focuses on the controls present in the process that is intended to either prevent or detect a problem and which may have been ineffective.
- Risk tree analysis and management oversight: One part of this strategy is using a tree diagram to examine what happened and its potential causes.
- Kepner-Tregoe Decision-Making and Problem Solving: This paradigm offers four unique stages for problem-solving:
- Analyzing the situation
- Analysis of the issue
- Solution evaluation
- Examination of potential issues
What Equipment Does Root Cause Analysis Use?
The five whys approach, Pareto charts, scatter diagrams, fishbone diagrams, and failure mode and effects analyses are some of the most well-known and often used root cause analysis tools.
1. Pareto Charts
The frequency and distribution of flaws and their cumulative effect are first shown on Pareto charts. The well-known 80/20 Pareto rule aids in examining potential fundamental causes of failures. As a result, it is highly effective at locating problems with the equipment or process obstructions.
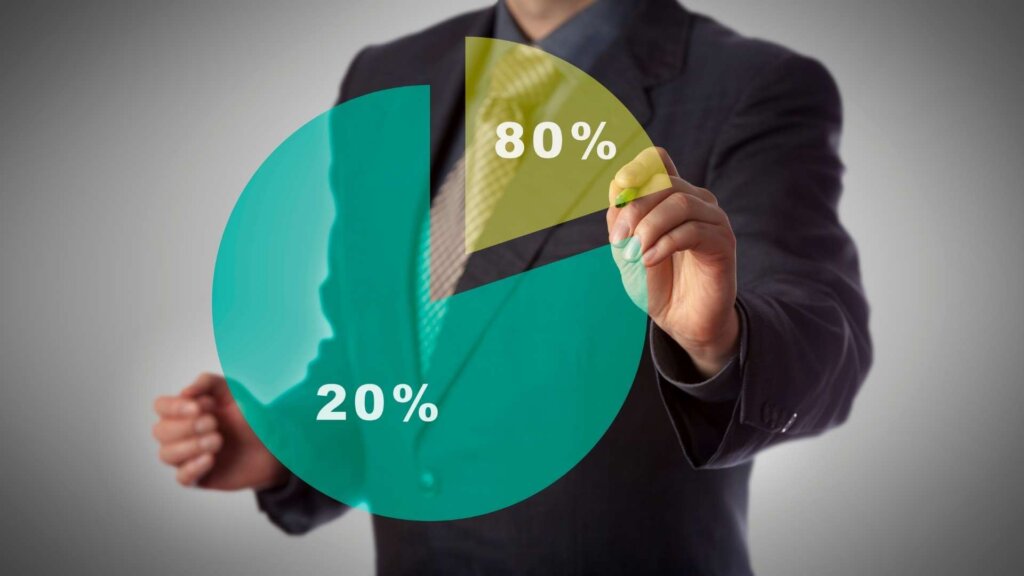
The Pareto chart ranks the identified flaws according to their seriousness and gives a more thorough description of the flaws that must be fixed first.
2. Five Whys
Second, one of the most effective problem-solving tools in the Lean toolbox is the 5 Whys analysis. It enables you to dissect an issue or an incident’s components in order to identify the underlying reasons.
The method suggests asking as many “Why” questions as necessary to determine the true cause. The 5 Whys method was developed in the manufacturing industry and is currently used in many industries when problems with people, technology, or processes arise.
3. Scatter Diagrams
Scatter diagrams are another technique for root cause analysis. The scatter diagram is a statistical method for displaying the association between two variables in a two-dimensional figure. The scatter diagram is used to pinpoint potential variation reasons by showing cause and effect in it.
4. Fishbone Diagrams
Fishbone diagrams are another tool used in root cause analysis. The fishbone diagram, sometimes referred to as the Ishikawa technique, is a diagram that resembles a fishbone and shows the various elements that can contribute to a problem, failure, or occurrence.
Where the fish’s head would be, the issue or incident would be displayed, and the fish’s backbone would serve as the cause.

Along the fish bones are illustrations of additional important variables. By visualizing the process in a diagram, the fishbone diagram method aids in idea generation, identifies process bottlenecks, and identifies areas for improvement.
5. Failure Mode and Effects Analysis
The root cause analysis method used by FMEA is preventive in nature. The approach uses data on past performance to forecast system problems in the future. For the analysis to determine a system’s risk priority number (RPN), input from safety and quality control teams is required.
The team must consider prospective disruptions, previous failure modes, and analysis of potential failure modes to arrive at this number. The FMEA method makes it easier to find a weak spot in a process or a system.
What Difficulties Does Root Cause Analysis Face?
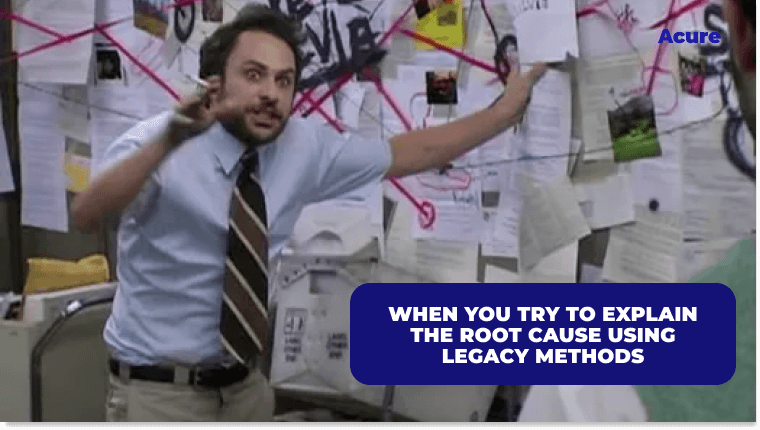
The root cause analysis method extensively uses data to develop a methodical approach to problem-solving. Inadequate and ineffective analysis of a process barrier can result from the absence of critical information.
On the other side, collecting data over a lengthy period of time might make it very difficult and time-consuming to pinpoint a harmful incident.
To assist you in differentiating between common and unique causes of problems, gathering information and creating a timeline of occurrences is crucial. Finding that a condition has multiple primary causes rather than just one is not unusual.
The root cause analysis approach can encounter difficulties when establishing a causal graph that displays several root causes.
How and in What Areas is RCA Used?
Root cause analysis may be used in a variety of settings and sectors thanks to its extensive toolkit, which gives businesses ways to solve problems and aid in decision-making. Healthcare, telecommunications, information technology, and manufacturing are a few industries that frequently use root cause analysis approaches.
Safety and Health
When examining events to identify the underlying causes of issues that resulted in undesirable results, such as patient injury or drug side effects, root cause analysis is used in the healthcare industry. The analysis is used to increase patient safety and take corrective action to stop similar situations from happening in the future.
IT and Telecommunications
Using root cause analysis methodologies in IT and telecommunications enables the identification of the underlying reasons for recently developed problematic services or resolving recurrent issues.
In procedures like incident management and security management, analysis is frequently applied.
Industrial and Manufacturing Process Control
In manufacturing, RCA is used to pinpoint the major reasons for maintenance or technical failure. The industrial process control discipline uses root cause analysis techniques to control chemical production quality.
Analysis of Systems
Because of its ability to solve problems, RCA has been successfully used to change management and risk management fields. RCA is perfect for system analysis since it can also be used to analyze firms, identify their objectives, and develop processes to achieve them.
Root Cause Analysis in Acure
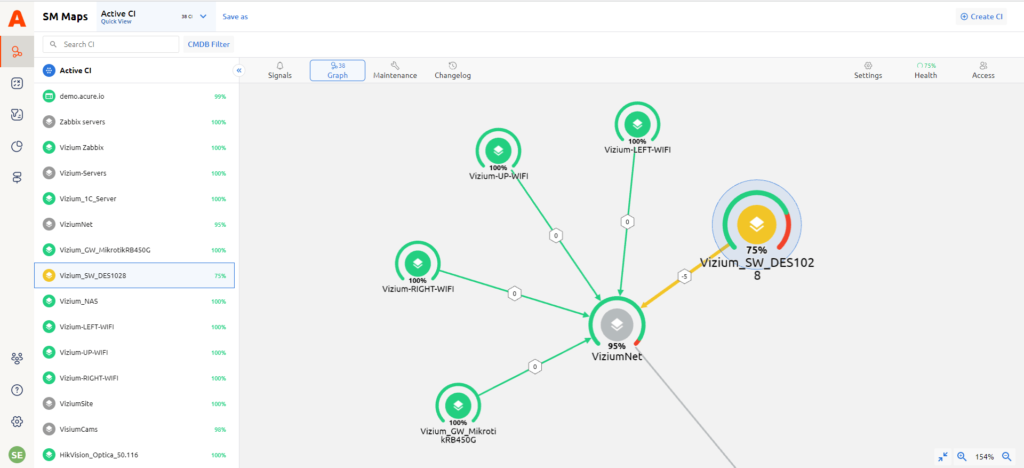
Root cause analysis in Acure is based on a topology tree that displays the IT infrastructure’s data from disparate sources. The topology includes configuration items and the relationships between them. Each configuration item contains information about the health and relationships with other elements of the system. The health of each item is calculated based on the health of the affected objects, as well as the monitoring events associated with it. The following are used as metrics:
- the weight of the connection — used in assessing the “equivalent” effect;
- a critical factor — the direct inheritance of health, suitable for critical nodes.
After any changes in the topology, the health of the system is instantly recalculated, coloring the entire tree appropriately.
If the health of the root configuration item turns red, you will see in detail which factors most negatively affect the object and go through the branches to eventually come to the element that affected the health of the entire system.